FAQ Help Center
Popular questions
FAQ
CNC lathe processing is a CNC processing technology, which can use the CNC system to control the movement of lathes, tapping and cutting tools to achieve the purpose of processing. The main principle of CNC lathe processing is to calculate the position, speed, angle and other parameters on a plane based on the configuration parameters input by the user (such as processing mode, cutting parameters, etc.), and then transmit the parameters to the CNC lathe controller. Control the movement of lathes, tapping and cutting tools to obtain the required machining accuracy and surface quality.
The principle of CNC lathe processing refers to the movement of the lathe, tapping and cutting tools through the program controller on the CNC lathe to obtain the required processing accuracy and surface quality. The steps of CNC lathe processing are roughly as follows:
1.Set program parameters: Set the motion parameters of lathe, tapping and cutting tools.
2.Control the movement of the lathe: According to the set parameters, control the position, speed and angle of the lathe to complete the processing requirements.
3.Control tool movement: According to the set parameters, control the position, speed and angle of the tool to complete the processing requirements.
4.Control the tapping movement: According to the set parameters, control the position, speed and angle of tapping to complete the processing requirements.
5.Complete processing: According to the above steps, complete the processing work and obtain the required processing accuracy and surface quality.
High precision: CNC lathes have high processing accuracy and can achieve micron-level processing accuracy to meet the processing needs of various high-precision workpieces.
High efficiency: CNC lathe processing has high-speed processing capabilities, which can achieve rapid, continuous, and batch production and improve production efficiency.
Flexibility: CNC lathe processing has strong processing adaptability and can be flexibly adjusted and processed according to the shape, size and processing requirements of different workpieces.
Automation: CNC lathe processing has automatic control functions, which can realize automatic tool changing, automatic measurement, automatic correction and other operations, reducing manual intervention and improving production efficiency.
Dataization: CNC lathe processing has a data management function, which can realize the collection, analysis and sharing of processing data, and improve the production management level and decision-making efficiency.
Aerospace: Used for processing aircraft engine parts, wing components and other aerospace components.
Automobile manufacturing: Used for processing automobile engines, gearboxes, suspension systems and other auto parts.
Shipbuilding: Used for processing shipbuilding parts such as ship propellers, hull structures, ship accessories, etc.
Construction machinery: Used to process key parts of construction machinery such as excavators, bulldozers, and cranes.
Precision instruments: Used for processing precision instruments, optical components, medical equipment and other precision parts.
With the continuous development of science and technology and the continuous progress of manufacturing industry, CNC lathe processing technology is also constantly evolving and improving. The future development trends mainly include the following aspects:
Intelligence: Strengthen the integration of CNC lathes with new technologies such as artificial intelligence and big data to achieve intelligent production and management.
Flexibility: Improve the flexibility and flexibility of CNC lathes to adapt to rapid changes in market demand and personalized customized production models.
Greening: Promote green manufacturing of CNC lathe processing, reduce energy consumption and environmental pollution, and achieve sustainable development.
High-end: Strengthen the research and development and innovation of CNC lathe processing technology, improve processing accuracy and efficiency, and meet the production needs of high-end products.
Internationalization: Strengthen international cooperation and exchanges, learn and absorb foreign advanced technology and experience, and improve the international competitiveness of CNC lathe processing technology.
CNC lathe processing is one of the important technologies in modern manufacturing industry, and its application will bring new opportunities and challenges to the development of manufacturing industry. By continuously strengthening research and innovation, we can better respond to these challenges and promote the development and application of CNC lathe processing technology.
Can’t find your answer?
Introduction to nouns
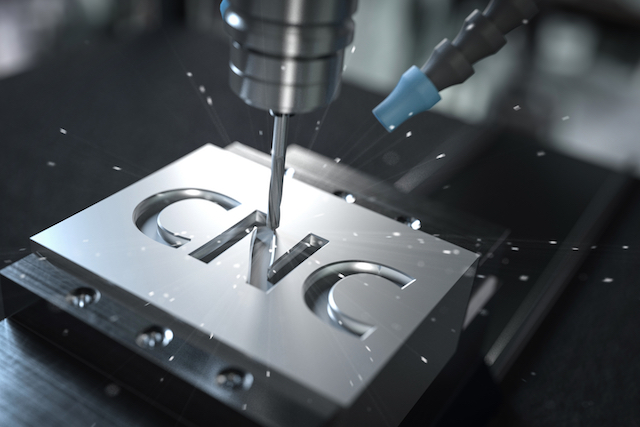
The lathe is a machine tool in the CNC machining process, and its history can be traced back to the ancient Egyptian period. During the Industrial Revolution, lathes played an important role and were therefore also known as the mother of all industries. During CNC lathe processing, the processing tool will be fixed on the lathe and rotate at high speed to cut the raw material until the processing is completed.
Lathes are used in a wide range of areas, including machinery manufacturing, metal processing, equipment maintenance, etc. CNC lathes are often used to assist in operations. The components that make up a lathe include a cast iron frame, a tool holder for surface cutting, various cutting tools, driving equipment, and control equipment. The electric motor operates at different speeds through the belts, machines, cams, and turntables of the transmission system to drive the entire drive equipment. Different lathes have different degrees of automation. When the operation of a lathe is driven by a computer program, it is called a CNC lathe.
The processing method of the lathe is that the workpiece rotates on the lathe itself, but the tool does not rotate on its own. A milling machine is the opposite of a lathe. The processing method of a milling machine is based on the rotation of the tool. The milling machine itself does not rotate. The raw material is cut through the rotation of the tool to complete the processing.
Milling machines are common industrial machines, so there are many types of milling machines. There are often only slight differences between different milling machines. Because of different processing purposes, designs or functions, different types of milling machines must be used. Milling machines are often used to drill and cut different materials. Generally speaking, the processing purposes achieved by using milling machines are similar to those of lathes. The main difference lies in the rotation of the machine tool.
Like lathes, milling machine operations can be performed manually or controlled by a computer. A computer-controlled milling machine is called a CNC milling machine, and a computer program controls the milling machine to complete the CNC machining process. There are many types of milling machines, such as vertical, horizontal, column, turret, bow frame (C type), bed type, gantry type, etc.
When using lathes or milling machines, different cutting tools must be used to complete the processing operations. They are divided into turning tools and milling cutters. Turning tools are suitable for cutting workpieces on lathes, while milling cutters are used for milling workpieces on milling machines. During CNC machining, the tool is fixed on a lathe or milling machine and material is removed to complete the process.
Turning tools are tools used on lathes for rotating, boring, grooving, and threading. Milling cutters and milling machines themselves move to complete milling. The tips of knives come in different shapes and sizes according to different needs.
End mills: End mills can mill at multiple angles, or mill along an axis. End mills can be used for contour milling, profile milling, surface milling, thread milling and other purposes.
Rough milling cutter: The rough milling cutter uses wavy teeth, which can be used to remove a large amount of material in the early stages of processing. The removed part will produce fragments and is easy to clean.
Ball milling cutter: A ball milling cutter is similar to a groove drill, but its milling cutter is hemispherical and is suitable for three-dimensional milling in the center, such as mold manufacturing.
First of all, the sizes of CNC engraving machines are different, and the types of motors they are suitable for are also different. Smaller CNC engraving machines are more suitable for using drive motors. Generally speaking, drive motors are more suitable for linear processing paths, such as belt drives, lead screws, ball screws and other smaller-scale jobs. On larger CNC engraving machines, it is easy to bend due to its larger size. In order to prevent deformation, it is more suitable to use a larger size and heavier servo motor.
The moving methods of the two motors are also different. The driving motor moves according to a predetermined number of steps. The machine itself cannot know the movement status of the driving motor. The movement status of the servo motor will be transmitted back to the machine, so the motor can be moved at any time. Are there any errors during operation?
In terms of speed and torque, the driving motor operates at about 1,200 RPM and can produce high torque at low speeds. The faster the speed, the smaller the torque. The servo motor can reach 2,000 RPM, has a higher speed than the drive motor, and has a higher torque than the drive motor.
Sandblasting technology uses high speed to force stainless steel sand to rub against the surface of the aluminum material, shaping the surface atomization process and producing a new oxide film to improve the anti-oxidation ability of the aluminum material. This is a destructive processing method that uses fine metal particles to impact the metal surface, causing granular depressions on the surface. Sandblasting is another processing before anodizing, so the aluminum after sandblasting also needs to be anodized or colored.
[wpgmza id=”1″]