FAQ Service Center
The Principle of CNC Machining
The main principle behind CNC machining is that computer-controlled machining tools bring the highest precision and repeatability. It starts with creating and converting a CAD drawing into CNC machine-readable instructions (G-code). Then. CNC machine controls their movements and operations with these digital instructions.
The CNC machine operates on multiple axes, from 3-axis (X, Y, and Z) to more advanced 5-axis machines. They can perform a variety of operations, including milling, drilling, turning, and grinding, depending on the machine’s capabilities.
If you have any questions, please feel free to interrupt.
CNC Machining Materials Options
The properties of final parts or products depend on the material type. Therefore, CNC machining material selection is critical for any project. Make your choice based on requirements, metals, plastics, or composites.
You have a lot of options for CNC metals such as aluminum, stainless steel, brass, titanium, etc. Consequently, each of these metals has different alloy grades with unique composition and properties. Meanwhile, You can machine CNC plastics like ABS, Acrylic, PEEK, PC, etc.
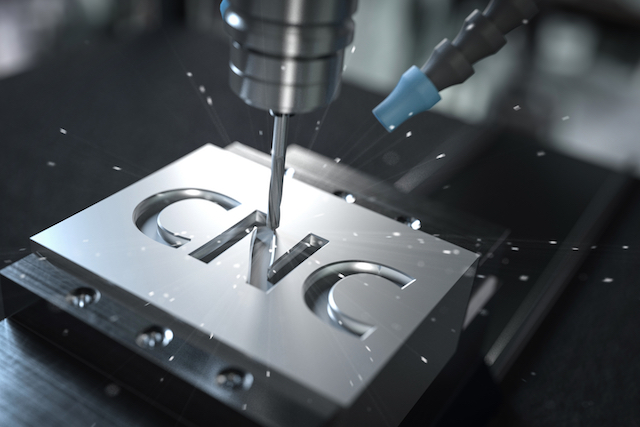